|
|
LE RAFFINAGE
 A) Les Techniques Il existe trois grandes familles d'opérations :
- La séparation : pour obtenir les différents types de produits des plus lourds aux plus légers.
- La transformation (ou conversion) : pour modifier les proportions naturelles des types de produits pour répondre à la demande des consommateurs.
- L'amélioration : pour éliminer les composants indésirables et modifier les caractéristiques de certains produits pour les rendre compatibles aux normes.
La séparation : Elle s'effectue par distillation fractionnée. Le pétrole est injecté à la base d une tour de soixante mètres de haut, appelé " topping " ou " colonne de distillation atmosphérique " (car la pression utilisée est proche de la pression atmosphérique). Là on chauffe à 350-400°C. La plus grande partie s'évapore et commence à monter dans la tour. Il ne reste à la base de la tour que les produits très lourds, les résidus. A mesure que les vapeurs montent, la température diminue. Il y aura des fractions de vapeurs (les plus lourdes) qui vont se condenser en liquide, ils seront récupérés sur des plateaux situés à différents niveaux de la tour. En haut de la tour (à une température de 150°C), on récupère les dernières vapeurs qui ne sont pas condensées : ce sont les gaz de pétrole. Ainsi, plusieurs types de produits différents (une dizaine environ) sont récupérés, des bitumes (les plus lourds) aux gaz (les plus légers). On appelle cela les " coupes pétrolières ". Mais à l'issue de cette première distillation, les résidus lourds ont su retenir une proportion notable de produits de densité moyenne. Ils sont donc soumis à une deuxième distillation plus poussée, mais cette fois sous vide. En haut de cette colonne, on récupérera du gazole, tandis qu'à sa base, on récupère des fiouls lourds.
La transformation (ou conversion) : les produits légers sont plus demandés sur le marché, mais la séparation donne des proportions considérables de lourds. Les molécules lourdes vont donc être cassées en petits morceaux. L'opération majeure de conversion de produits lourds en produits légers s'appelle le craquage catalytique. Il s'effectue à haute température (500°C), en présence d'un catalyseur (c'est-une substance favorisant les réactions chimiques sans y participer directement). Ce traitement est très énergique : plus de 75% des produits lourds sont transformés en gaz, essence et gazole. |
| 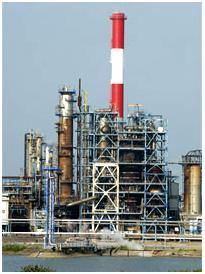 | Cette photo représente l'unité de craquage catalytique de la raffinerie de Donges.
|
| L'opération est encore plus efficace si on ajoute de l'hydrogène (hydrocraquage) et si on fait intervenir des procédés d'extraction du carbone (conversion profonde). Ainsi, tous les lourds sont transformables en légers, mais cette manoeuvre est coûteuse. Ces conversions profondes consomment une grosse quantité d'énergie.
L'amélioration : les produits issus de la distillation et de la conversion doivent être débarrassés de molécules corrosives ou néfastes à l'environnement, en particulier le soufre.
|
| La désulfuration du gazole : elle s'effectue à 370 °C, en présence d'hydrogène et avec une pression de 60 bars. Les atomes de soufre quittent les hydrocarbures pour l'hydrogène en donnant du sulfure d'hydrogène H2S. Ce dernier sera ensuite traité pour donner du soufre, qui, autrefois, formait de gros tas jaunes visibles dans certaines raffineries. Aujourd'hui le soufre est stocké dans des réservoirs maintenus en température afin de le garder liquide. Les normes européennes sur les émissions de soufre dans l'atmosphère sont très sévères : les raffineurs doivent repenser et réformer leurs unités de désulfuration pour abaisser encore la teneur en soufre des carburants.
|
| 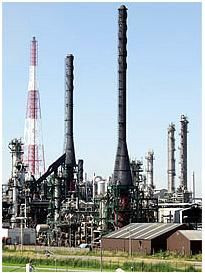 | La photo ci-dessus représente l'unité de désulfuration de la raffinerie d'Anvers en Belgique.
|
| D'autre part, certains produits, comme les essences, ne peuvent pas être utilisés directement dans les moteurs à cause de leurs propriétés détonantes dues à leur indice d'octane trop faible. L'indice d'octane mesure la capacité antidétonante d'une essence ou d'un super. Plus il est proche de 100, plus les propriétés détonantes diminues. Le 95 et le 98 représentent l'indice d'octane. Les moteurs avec des taux de compression très élevés, ont un besoin d'essences à haut indice d'octane.
Le reformage catalytique est la principale opération permettant d'augmenter l'indice d'octane.
Pour obtenir un bon produit à la fin du raffinage l'essence passe dans quatre réacteurs successifs à une température de 500°C, sous une pression de 10 bars et comme catalyseur, du platine. D'autres méthodes permettent l'amélioration de l'indice d'octane : l'alkylation*, production d'éthers MTBE et ETBE à haut pouvoir antidétonant.
L'adoucissement est un procédé d'amélioration, destiné cette fois aux gaz butane et propane et au kérosène : On lave les produits à la soude pour les débarrasser des mercaptans, produits soufrés nauséabonds et corrosifs (un mercaptan R-S-H est un alcool où l'atome de soufre occupe la place de l'atome d'oxygène).
|
|  B) Le dessalage | Le pétrole brut contient souvent de l'eau, des sels inorganiques, des solides en suspension et des traces de métaux solubles dans l'eau.
La première étape du raffinage consiste à éliminer ces contaminants par dessalage (déshydratation) pour réduire la corrosion, le colmatage et l'encrassement des installations et empêcher l'empoisonnement des catalyseurs dans les unités de production. Le dessalage chimique, la séparation électrostatique et la filtration sont trois méthodes typiques du dessalage du pétrole brut.
Dans le dessalage chimique, on ajoute de l'eau et des agents tensio-actifs (désémulsifiants) au pétrole brut, on chauffe pour dissoudre ou fixer à l'eau les sels et les autres impuretés, puis on conserve ce mélange dans un bac pour que la phase aqueuse décante.
Le dessalage électrostatique, on applique des charges électrostatiques de tension élevée pour concentrer les gouttelettes en suspension dans la partie inférieure du bac de décantation. On ajoute des agents tensio-actifs uniquement lorsque le pétrole brut renferme beaucoup de solides en suspension. Un troisième procédé, moins courant consiste à filtrer le pétrole brut chaud sur de la terre à diatomées. Il s'agit de la filtration.
Dans les dessalages chimique et électrostatique, on chauffe la matière première brute jusqu'à une température comprise entre 66°C et 177°C, pour réduire la viscosité et la tension superficielle et faciliter ainsi le mélange et la séparation de l'eau ; la température est limitée par la pression de vapeur du pétrole brut. Ces deux méthodes de dessalage sont réalisées en continu. Une base ou un acide sont parfois ajoutés pour ajuster le pH de l'eau de lavage ; on peut aussi ajouter de l'ammoniac pour réduire la corrosion. Les eaux usées et les contaminants qu'elles contiennent sont repris à la partie inférieure du bac de décantation et acheminés vers l'unité d'épuration des eaux usées. Le pétrole brut dessalé est récupéré en continu à la partie supérieure du bac de décantation et envoyé à une tour de distillation atmosphérique (tour de fractionnement).
Si le dessalage est imparfait, il y aura encrassement des tubes réchauffeurs et des échangeurs de chaleurs dans toutes les unités de la raffinerie, ce qui se traduira par une diminution des débits dans les circuits et une réduction de la vitesse de transfert de chaleur et causera des défaillances en raison d'une augmentation de la pression et de la température. Toute surpression dans les unités de dessalage provoquera une panne. La corrosion due à la présence de sulfure d'hydrogène (H2S), de chlorure d'hydrogène (HCl) et d'acides naphténiques provoquera aussi des défaillances. On parle de corrosion lorsque des sels neutralisés (chlorure et sulfure d'ammonium) entrent en contact avec de l'eau de condensation.
Dans le procédé de dessalage, il existe une phase composée d'eau, de sels minéraux et d'hydrocarbures qui stagnent au fond des dessaleurs. Ce sont des slops.
| 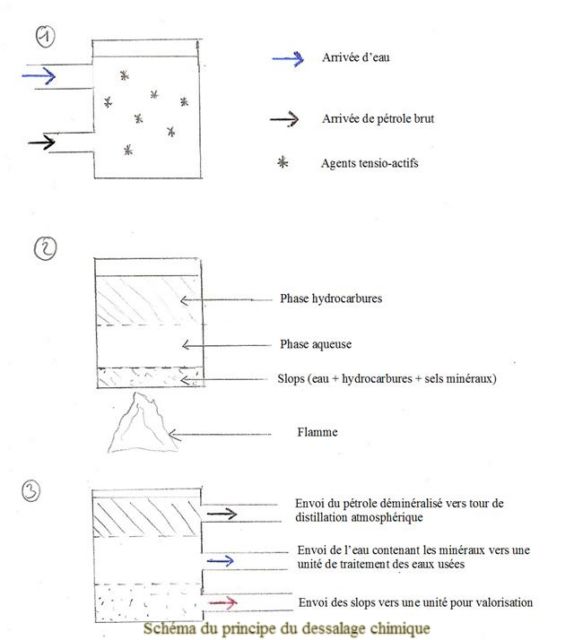 |
|
|
Copyright © 2009. Tous droits réservés. Lycée de Montgeron samedi 7 février 2009 | Contactez les auteurs à adrienkhetir@free.fr |
|
|
|